In case you missed it, MEB’s Preconstruction Manager Tim Ratay, PE, DBIA, presented at this year’s WaterJAM conference in Virginia Beach, Virginia. Todd Pollick from C&B Piping, one of our suppliers, joined Tim to present from a supplier’s perspective. The presentation focused on preconstruction strategies to identify early construction needs, accelerate procurement to release long lead items, and how Owner, Designer, Contractor, and Supplier collaboration can improve the schedule.
While improving, we are still experiencing unstable lead times, causing extended delivery dates that lengthen the project schedule and increase the project risk profile. Through our experience with this, we have found methods to try and combat those to the best of our ability.
Implementation Strategies touched on in the presentation include:
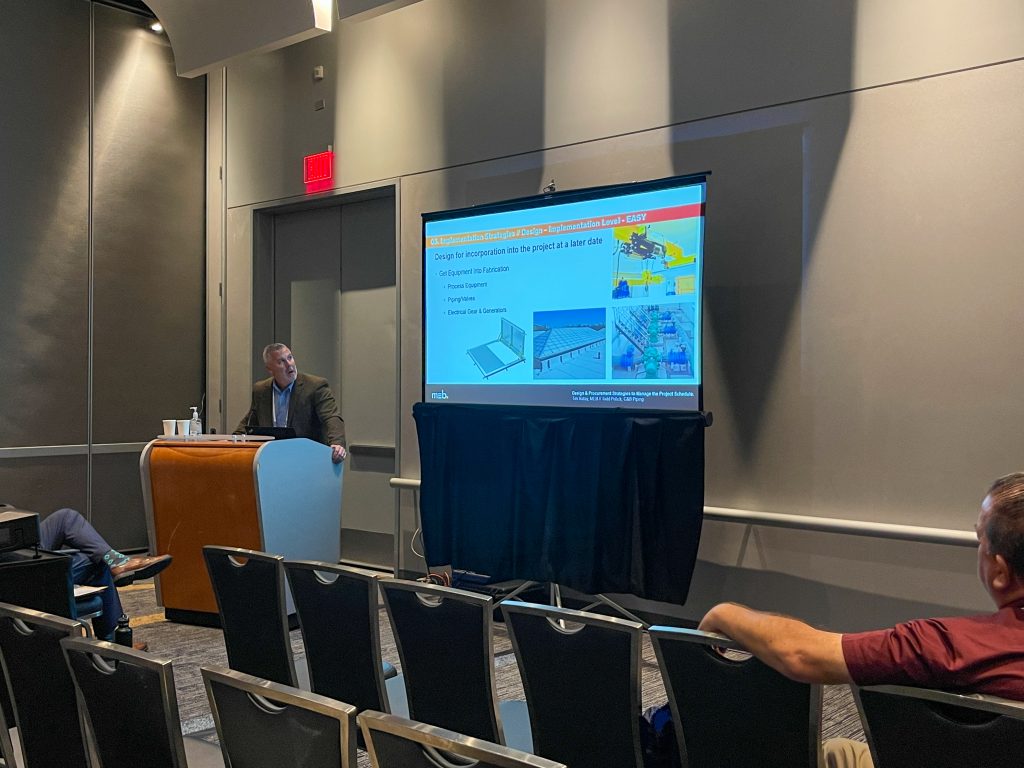
1. Design for incorporation into the project at a later date so equipment can get into fabrication early.
2. Accelerated Design strategies to identify early construction needs such as deep foundations and in/under piping to get those released early to accelerate concrete construction.
3. Conservative Designs like upsizing and lengthening test piles can help get material to the jobsite earlier; if you’re in between sizes during design – opt for the larger one to expedite fabrication and delivery.
4. Consider material alternatives – for example – for deep foundations consider Auger Cast Piles vs. Driven Piles. Design for “off the shelf” products that stay in stock to avoid lead times.
5. Collaborate with suppliers and designers to incorporate phased submittals and phased production to break up equipment packages to focus on schedule-critical items.
6. Early supplier/subcontractor selection and involvement.
7. Advocate for an in-person and early permitting meeting with all permitting agencies.
8. Breakout designs into phased packages to accelerate construction start. For example – Package 1 – site, Package 2 – foundation, and Package 3 – Building.
We’ve found that these strategies are best used on short-duration projects (24-30 months), fast-track/non-linear projects, scheduled shutdowns (seasonal outages), and phased projects.
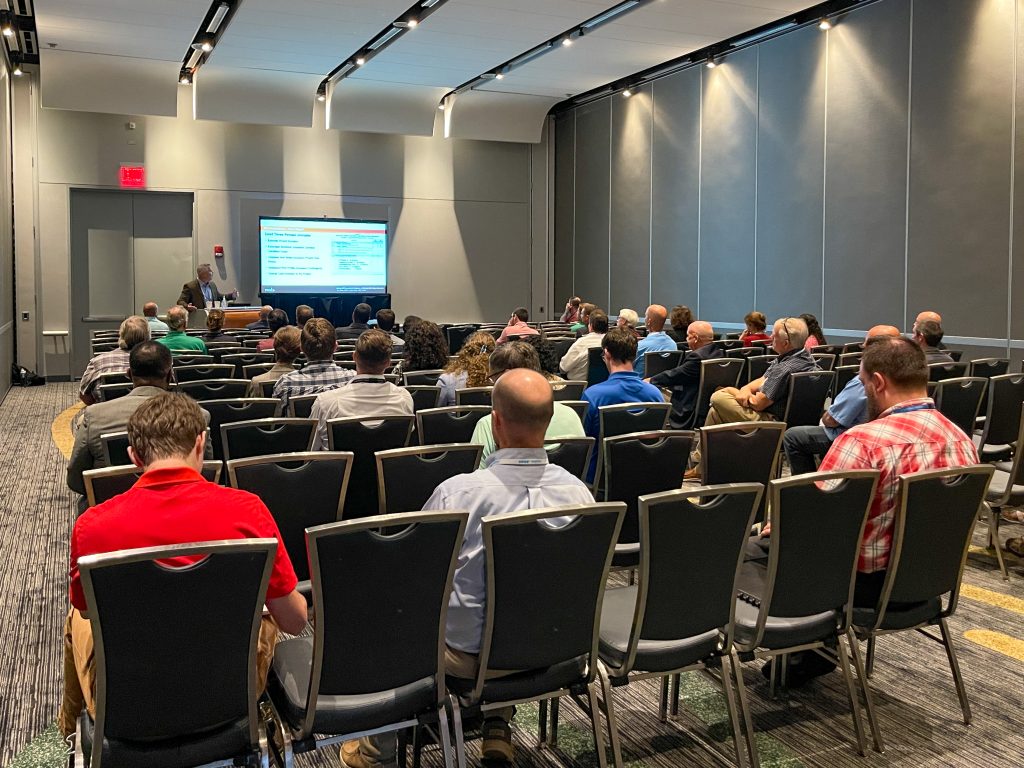
While this presentation only scratched the surface of potential strategies to improve the schedule, the key takeaway is there is not a one-size-fits-all approach. Implementing strategies like these requires early engagement and collaboration from all project members and stakeholders. Defining client objectives, schedule challenges, and associated risks early in the project is essential. Todd and Tim both agree that early collaboration and open communication between the project team members and suppliers can reduce long lead times and accelerate upfront construction needs.